Interview with Wiebe Schipper, Vice President of European and Asia Pacific Operations, PureCycle.
As the EU moves closer to implementing the Packaging and Packaging Waste Regulation (PPWR), technologies that can produce high-quality recycled materials at scale are more important than ever.
PureCycle is one company leading the way, leveraging a proprietary dissolution-based purification process to transform post-consumer polypropylene (PP) waste into high-quality recycled PP (rPP).
We spoke about how their technology and approach supports PPWR goals, what’s needed to scale in Europe, and the challenges ahead.
What are the key benefits of dissolution recycling in helping companies comply with PPWR and advance the circular economy for flexible packaging?
While mechanical recycling has made progress in recovering polypropylene for select applications, it often struggles with quality limitations. PureCycle’s proprietary dissolution recycling process offers a transformative solution by removing colour, odour, additives, and other contaminants from post-consumer PP. This results in high-purity rPP that performs comparably to virgin material.
Our process expands the potential use of recycled PP into sectors that traditionally require stringent performance characteristics. We’ve partnered with leading players across automotive, fibre, and packaging industries, successfully trialling and producing products with our PureFive™ rPP.
As regulatory frameworks and corporate targets push for higher levels of recycled content, PureCycle offers a high-yield, scalable, and lower-carbon alternative to virgin PP, helping companies to meet both compliance requirements and sustainability goals.
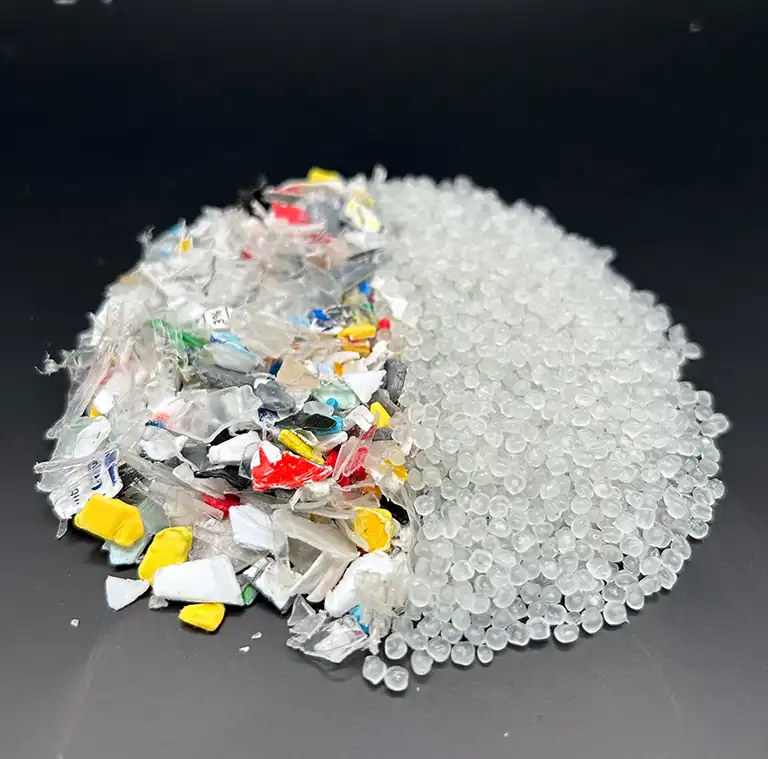
Post-Consumer Curbside Flake with PureCycle’s PureFive™ rPP
What are the critical enablers needed to maximise the impact of your technology in Europe by 2030?
Several enablers are essential to successfully scale in Europe. First and foremost, the continued evolution of Extended Producer Responsibility (EPR) legislation and clear compliance mechanisms under PPWR will be crucial. These regulatory drivers will incentivise investment and accelerate market uptake.
We also see strategic partnerships as key. We are actively collaborating with brands focused on sustainable goods, as well as with recycling operators and feedstock collectors to ensure a robust supply chain and broad applicability for our rPP.
Equally important is education and visibility. Increasing awareness of what dissolution recycling can achieve, particularly in terms of quality and performance, will help build support from both policymakers and industry leaders. We are already seeing some of that recognition, and the EU’s Clean Industrial Deal for example contains several financial instruments and frameworks that may also support the expansion of innovative recycling solutions like ours across the region.
What are the biggest challenges or barriers to scaling your technology, and how can they be overcome?
Like most novel recycling technologies, challenges include securing attractive financing for scale-up projects; obtaining regulatory approvals, such as from the European Food Safety Authority (EFSA); and building customer confidence and demand for our rPP across different applications.
Fortunately, our operational success at our Ironton, Ohio facility in the U.S. has helped strengthen our financial positioning and validate the technology. In Europe, we are actively pursuing funding from mechanisms such as the European Innovation Fund, along with regional support in Flanders.
On the regulatory front, we’ve already received FDA letters of no objection in the U.S. for food-contact applications and are now working toward EFSA approval in Europe. Extensive testing and material trials will be underway soon to ensure our PureFive™ rPP meets all EFSA criteria.
In terms of operations, project development of our first European facility is underway in Antwerp, Belgium. The site will initially have a production capacity of 59,000 tonnes a year of rPP and has space to significantly expand capacity in future phases. We are currently engaging with European customers and feedstock suppliers in various stages of product testing and qualification, with the aim of positioning PureFive™ as a drop-in solution for virgin PP in a broad range of applications.
“PureCycle’s European expansion comes at a critical moment for packaging and plastic recycling. With the right regulatory support, partnerships, and investment, its technology could help shape a more circular and resilient future for polypropylene”
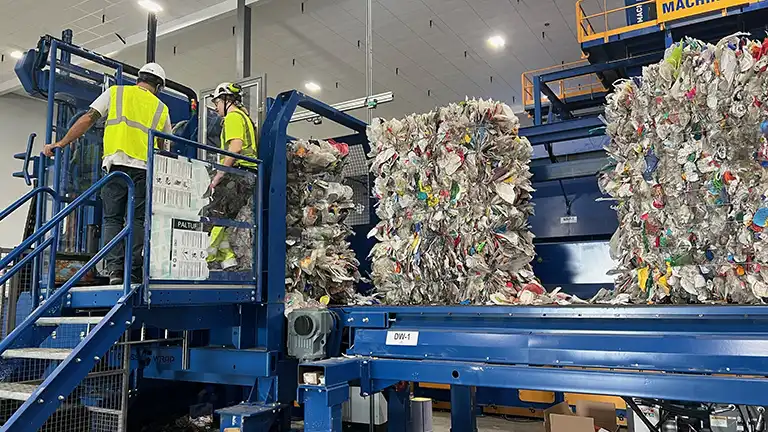
Sorting at PureCycle’s site in Denver Pennsylvania, United States
Wiebe Schipper,
Vice President of European and Asia Pacific Operations, PureCycle