How can mechanical & chemical recycling work together in practice to achieve full material circularity
A well-functioning ecosystem will require the full range of tools to achieve packaging circularity, which includes design for recycling and eco-efficiency; re-use models, and multiple recycling pathways.
Stephan Roest, Strategic Business Platform Leader – Circular Economy Solutions (CES) at Borealis, talks about the importance of a cascade model and shares his thoughts on the actions needed to support the transition to a circular economy.
Can you shed some light on the synergies between mechanical and chemical recycling and the possible outcomes for a circular economy?
Let me start by saying that circularity demands a 360-degree approach and keeping this in mind, we have developed a circular cascade model. It supports the optimisation of product design for reuse and recycling and recognises the complementary role of mechanical and chemical recycling technologies.
In practice, this complementarity equates to a sequential approach of first mechanically recycling post-consumer plastic waste and then chemically recycling the fractions which can’t be mechanically recycled; either because the demand for mechanical recyclate is saturated or because the end markets require food contact quality. Both technologies play an important role in closing the plastics loop once the product reaches its end of life.
If I talk about recycling of flexible packaging, Borealis and Ecoplast have demonstrated that mechanical recycling of flexible polyolefins can yield good quality recyclates. We have also been part of the CEFLEX ‘Quality Recycling Process’ action team in this vein. However, for heavily printed or coloured films and other residual waste streams rejected by mechanical recycling processes, chemical recycling can be a good solution.
Another reason why chemical recycling plays its role within the cascade is in the production of recycled plastic for food contact applications. With processes like pyrolysis, we have seen that we can produce virgin-equivalent polymers for such applications.
So, to drive the best outcome for a circular economy, my recommendation would be to work with an integrated approach, which can sort and pre-treat the waste streams. As an example, let’s look at our partner Renasci’s Smart Chain Processing concept. This advanced model enables the efficient processing of low-quality mixed waste streams – metals, plastics, organic waste – and maximises material recovery by using a mix of state-of-the-art sorting and recycling technologies, including chemical recycling of the mixed plastic waste stream.
In your view, what are the main challenges and opportunities specifically for flexible packaging?
In the case of flexible packaging, a majority of plastic waste doesn’t get recycled today. Also, most of the end markets such as food-contact applications, demand high quality. Chemical recycling technologies have opened the possibility to recycle this waste back into a film, which can have multiple lifetimes. For polyolefins specifically, their use in direct food-contact packaging and applications is possible with chemical recycling, or by using renewable feedstock.
What steps are needed to set up an ecosystem where all recycling technologies can work together effectively?
That’s an interesting question, and I think the full answer is currently tied to a couple of open questions such as:
Does the ecosystem need to be close to the waste source or to the plastic processing unit?
Do we process everything locally?
For now, I find the concept of an integrated approach for sorting and pre-processing waste streams to be very useful. The high-quality plastic waste fractions can be sent for further processing via mechanical recycling and the rest, to chemical recycling plants.
Of course, higher waste collection rates will be needed to continuously feed such an integrated plant.
Overall, a well-functioning ecosystem will require the full cascade of plastic circularity. It starts with the proper design for recycling, design for eco-efficiency, and re-use models, and is followed by high quality mechanical and chemical recycling at the end of the product lifecycle.
Are there any roadblocks to achieving such an ecosystem?
From a regulatory standpoint, chemical recycling technologies need full recognition. Along with this, the policy framework should also support the mass balance approach for the allocation of recycled content to the end product. Here, the value chain must work together to provide more clarity on these topics to the policymakers, NGOs, and the general public. Industry associations too can especially play a vital role in driving more awareness.
Another challenge is with regards to the scaling up of new technologies as the industry adapts to totally new feedstocks like different types of plastic waste, mixed waste or several types of renewable feedstock.
What are the possible scenarios ahead to achieve full material circularity?
I believe that higher collection, sorting and recycling rates can only be possible with the right regulatory environment and coordinated actions by all the actors in the value chain. The downstream players, for example, can help by incorporating more recycled content in their new products and by implementing design for recycling guidelines. And if fee modulation is applied within the Extended Producer Responsibility (EPR) system, it will further incentivise eco-design.
At Borealis, as part of our mission to support the transition to a circular economy, we are constantly looking to increase the amount of alternative sustainable feedstocks to produce our plastics. Alternate sources currently on our radar include not just chemical recycling, but also renewables and feedstock from carbon capture & utilisation (CCU) technologies.
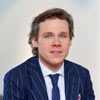
Stephan Roest,
Borealis