How can mechanical and chemical recycling work together in practice to achieve full material circularity?
For flexible packaging, implementing an appropriate mix of mechanical and chemical recycling technologies will be key to advancing the circular economy. Dana Mosora helps us understand what this would mean in practice and shares her insights on the road ahead to setting up the required ecosystem.
Can you shed some light on the synergies between mechanical and chemical recycling and the possible outcomes for a circular economy?
Flexible packaging can take major steps to achieving circularity with the complimentary application of mechanical and chemical recycling technologies. A lot can be accomplished with the continued enhancement of mechanical recycling processes and the redesign of flexible packaging to maximize recyclability – for example, mono-material packaging. However, we need to be mindful of the fact that everything cannot be redesigned. For certain demanding applications, multi-material solutions might still be the best option to meet performance requirements. For such cases, chemical recycling can offer a viable solution where mechanical cannot.
The suitability of the recycling technology also depends on the other important factors like the level and the nature of contamination of the available waste feedstock and the end-use market. For instance, for food-contact applications, the current legislative framework in EU doesn’t accept mechanically recycled polyolefins.
We should, therefore, evaluate the benefits and limitations of the available recycling technologies to achieve the best value possible. I would also like to highlight here that chemical recycling cannot accept everything that mechanical recycling cannot but definitely for certain feedstocks and specific applications, chemical recycling is the preferred option.
In your view, what are the main challenges and opportunities specifically for flexible packaging?
The number one challenge is achieving the right balance of quantity and quality for the waste feedstock. Currently, there isn’t enough collection of flexible packaging and often co-mingled waste is collected. If the feedstock is not available in sufficient quantities, the economics for recycling will be unfavourable. And there is also a need to minimize the contamination at source. Both these issues can be solved by setting up best practices for collection to get the feedstock in the right form, which will enable higher quality of recyclates.The second challenge is to ensure that the money is put in the right place. The question we must ask is “does the current technology bring the best value possible?”.
For instance, with the Quality Recycling Process (QRP), we have seen that value driven recycling of PP film is possible when the adequate and fit for purpose infrastructure and technology are in place. Similarly, when fully funded chemical recycling can uplift the value of the recyclates and make them fit for regulated sectors such as food-contact applications. Investing in the adequate infrastructure and new innovative technologies should, therefore, continue.
And finally, the third big challenge is the absence of a clear legal framework with regards to chemical recycling technologies. Regulatory bodies have expressed concern regarding their environmental footprint of chemical recycling. The way forward is to align on clear boundaries for the assessment of the environmental impact, within which these technologies should meet the necessary environmental targets. These should be based on the scientific comparison of clear and precise data, which can help understand the impact in relation to virgin polymer production and existing end-of-life solutions like landfill and incineration.
Chemical recycling technologies are ready to be commercialised and further R&D development and scale-up demands more investment. But, if the legislation continues to remain unclear with respect to the boundaries of chemical recycling, the investment may start to dry up.
What steps are needed to set up an ecosystem where all recycling technologies can work together effectively?
Value chain collaborations must foster a united front. The common goal should be to create packaging with the best design, which meets the performance requirements and is recycled at the end of life via the most suitable recycling technology to achieve the highest value possible so that it can be used again in new market applications. In regards to recycling, we need to continue to upgrade existing technologies and develop new solutions in parallel. Platforms specifically designed to test new ideas, concepts, and technologies and assess their commercial viability can facilitate this. For instance, at CEFLEX, while working on QRP, we collaborated with the National Test Centre for Circular Plastics (NTCP) based in the Netherlands. Making more such platforms and research centres available across Europe will help accelerate innovation and support more projects towards better recycling of plastics.
Overall, I would say we need investments in the right infrastructure and technologies to ensure the best possible value. And such investments will require adequate support from legislation.
Are there any roadblocks to achieving such an ecosystem?
Lastly, I hope that the EU rules on transporting waste within and beyond EU borders will not create any unnecessary barriers going forward.
What are the possible scenarios ahead to achieve full material circularity?
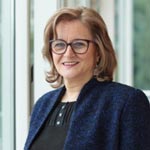
Dana Mosora,
Workstream Consultant, CEFLEX