Creating, planning and investing in meaningful synergies starts today… #MissionCircular spoke with Clemens Kitzberger and Klaus Lederer of EREMA Group to help unpack how they work together to boost circularity.
From taking the decision to set up a new recycling plant to the production of the first batch of recyclates may take 2-4 years. Regulatory approvals, internal decisions related to technology and finance, sourcing of input material stream, etc., require a lot of time. Keeping the upcoming EU recycling targets for 2025 and 2030 in mind, it will be critical to take such decisions as early as possible to put the required infrastructure in place to produce the required quantities of recycled materials.
To further analyse the role of different recycling technologies and understand the technical advances and challenges that lie ahead, we spoke with Clemens Kitzberger, Post Consumer Business Development Manager, and Klaus Lederer, Technology Research Manager Chemical Recycling at EREMA Group.
Can you shed some light on the synergies between mechanical and chemical recycling and the possible outcomes for a circular economy?
CK: Everything starts with design for recycling. This will benefit both mechanical and chemical recycling. The general perception, initially, was that chemical recycling can accept any feedstock with minimum or no pre-processing. However, we’ve learned over the past few years that the input feedstock for chemical recycling also needs to meet certain specifications. This means that mechanical material preparation technologies such as sorting, cleaning, and melt-extrusion will be a major contributor to the success of chemical recycling operations.While chemical recycling may be the solution for difficult to recycle waste streams, mechanical recycling will be the preferred solution in most cases due to economic and environmental impact reasons. Also, the continued development of solvent-based recycling and purification technologies will play a key role in the transition to a circular economy.
KL: We can expect prioritisation of recycling and conversion technologies to be according to their GHG contribution and capability to keep energy already introduced into the system in the loop. The smaller the step back in the plastic value chain, the better.
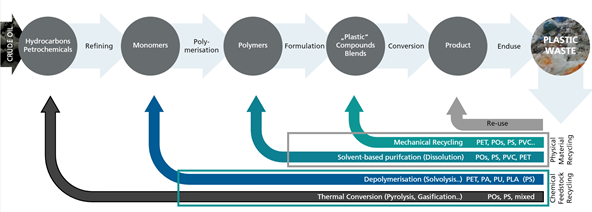
Image credit: Klaus Lederer, EREMA Group
The actual complementarity will strongly depend on the future ability of chemical recycling technologies to work with plastic waste feedstocks that cannot be recycled mechanically and currently end up in incineration or landfill.
For instance, multilayer films would be the logical target material for chemical recyclers. Typical polyolefin content in multilayer films is not high enough to call it a good feedstock for chemical recycling operations i.e. typically pyrolysis, the most common thermal conversion technology. Redesigning multi-layer packaging with mono-materials will help to make polyolefin-rich feedstocks available in sufficient quantity so that they don’t compete with mechanical recycling, is key to many chemical recycling operations and another crucial factor for complementarity of mechanical and chemical recycling.
In your view, what are the main challenges and opportunities specifically for flexible packaging?
CK: Packaging designers have been using colour and unique designs to attract consumers and often, flexible packaging contains components such as printing ink and labels that provide important information. These designs need to be optimized according to design for recycling guidelines, which can further improve the recycling rate and quality of recyclates.It is good to take inspiration from existing flexible packaging design examples that can easily be recycled mechanically. For instance, stretch and shrink films that are used as secondary packaging in supermarkets. These films are usually neither printed nor coloured and the only contamination is in the form of a paper label. Such films can be readily mechanically recycled to produce new shrink films with up to 50% recycled content! This exists today and the economics work well with the supermarkets getting paid by material recovery facilities to collect these films.
We also see continued advances in mechanical recycling processes. For instance, with the Quality Recycling Process (QRP), shrink films with 30% natural rPE content – obtained via mechanical recycling – have shown good performance. With continued development, I expect that the recycled content can be further enhanced to 70% possibly in the future. Also, to counter the issue of down-cycling, petrochemical companies have developed innovative additives that allow the material to stay in the loop longer.
What steps are needed to set up an ecosystem where all recycling technologies can work together effectively?
CK: Multiple steps and coordinated actions are required. More investments will be needed to set up high-end recycling plants and the industry must adopt and implement the design for recycling guidelines.A lot of work is also required to improve the collection and sorting of plastic waste. We must ensure standardised collection schemes and consumer education strategies for harmonised collection of all flexible packaging waste with minimum contamination. Implementing these measures in combination with advanced sorting technologies can significantly increase the production quantities of recyclates that can be used in demanding end market applications.
And finally, we need a supporting regulatory environment based on transparent data and scientific facts. The regulations must take into account all packaging materials – not only plastics but also paper, aluminium, etc. – to avoid the introduction of recyclable packaging compositions but which have a higher cost and environmental impact that the ones they replace coming into the market. A close collaboration between the industry and the legislative bodies will play a vital role here.
Are there any roadblocks to achieving such an ecosystem?
CK: For certain demanding applications, mono-material packaging – though, compliant with design for recycling guidelines – may not be suitable to meet the performance standard required by the product. Further advances in design and materials will be needed to replicate the functionality of today’s multi-material packaging.Additionally, when setting up new plastics recycling plants, a lot of time is needed for regulatory approvals, internal decisions related to technology and finance, sourcing of input material stream for business modelling, and so on. This can delay the readiness of such an ecosystem. From taking the decision to set up a new greenfield recycling plant to the production of the first batch of recyclates may take 2-3 years for mechanical recycling operations. For chemical recycling – typically, plants where post-consumer flexible packaging can be fed & prepared for pyrolysis – it can take up to 3-4 years. Keeping the upcoming EU recycling targets for 2025 and 2030 in mind, it will be critical to take such decisions as early as possible to put the required infrastructure in place to produce the required quantities of recycled content.
KL: With regards to chemical recycling, while potentially large-scale plants could be significant contributors, their role currently remains somewhat unclear. This is due to open legislative discussions in terms of economic feasibility and whether the recycled materials count towards the EU recycling targets.
What are the possible scenarios ahead to achieve full material circularity?
CK: PET bottles industry is a good example to follow. As per a recent report published by Eunomia, 2.2mt of PET bottle bales were sorted for recycling in 2020. This roughly equates to a sorted for recycling rate of 61% for PET bottles in Europe. Coordinated actions by all actors in the PET bottles value chain have played an important role. Applying these best practices can help us move closer to the desired outcomes for flexible packaging.It is important to close the loop wherever possible so that material can be returned to the economy to be reused again and again.
Lastly, it is important that we assess the full life cycle of a packaging and compare common evaluation parameters. Analysing and comparing Product Carbon Footprint (PCF) is one of the leading solutions to enable a level playing field.
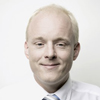
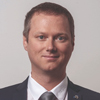
Clemens Kitzberger & Klaus Lederer
EREMA Group