NTCP is an exciting new test bed for sorting and recycling plastics, how did it come about and what are the key competences and facilities onsite?
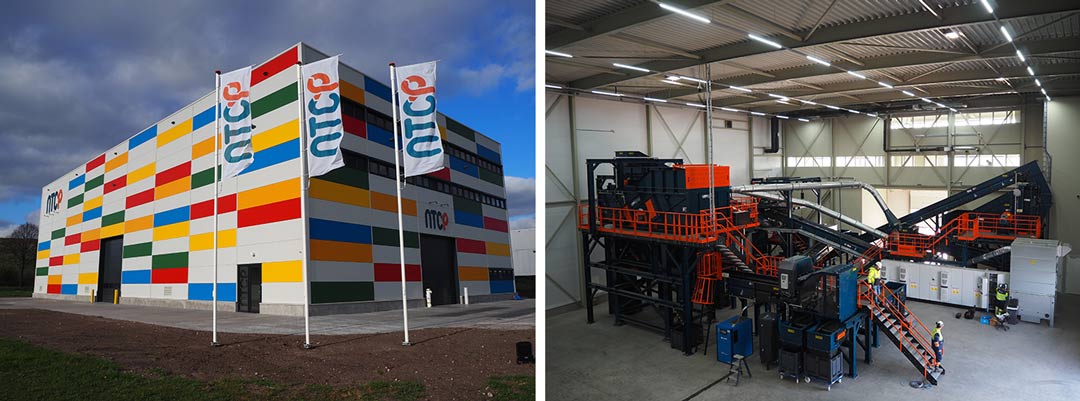
Conception of the NTCP site started in January 2019 and the complete facility has been operational since mid-April 2020. In addition to industrial scale facilities, NTCP has different types of lab equipment to be used for compositional analyses on a flake level and detailed material analysis (FT-IR, NIR).
At this point in time, we already performed projects for and with all different stakeholders (brand owners, retailers, packaging developers, sorters, recyclers, technology developers, policy makers).
Our industrial scale sorting line is fully customised for testing and R&D. The uniqueness is that we work in a fully controlled environment, using real waste streams. All process steps one can find in industrials sorting installation are present in the NTCP sorting line; drum feeder, screen, wind shifter, magnet, ballistic separator, non-ferro separation, optical sorter.
But what is truly unique, is our ability to fully control the scope and settings across the whole line. At every step in the process, either the positive or negative sorted material can be extracted for sampling and analysis… and we can also turn off individual process steps.
At NTCP material can run in a loop thanks to open ‘innovation’ positions in the sorting line, where new technologies can be physically implemented and evaluated. Due to this modular design, NTCP is able to develop new sorting protocols and re-route the material across the different sorting technologies to determine how we can get the best results with the least amount of effort.
Our line can run at around 2000 kg/hour for mixed plastic waste (rigid and film combined).
We currently also have a small washing setup (max 30kg scale) to prepare lab scale cold and/or hot wash samples and preparing an industrial size washing line in our facility, including all relevant washing steps from based on the same principles as the sorting line (modular, fully customised for tests and R&D) with a foreseen capacity of 500kg/hour.
How are you collaborating with CEFLEX and how can this work help accelerate a circular economy for flexible packaging?
This reverse engineering approach – exploring the end-user market back into design, sorting and treatment (washing, extruding) – matches really well with our vision of ‘application driven sorting and recycling’ and a shared ambition to make a substantial step forward in this space. Creating a deep understanding of the sorting process and future application of recyclate in new and existing end markets is a vital next step in creating a circular economy, and we are delighted to be tackling this challenge together with CEFLEX.
From our perspective, the experience and results prove a couple of important things needed to develop and deliver these types of integral projects:
First, cooperation and understanding between all disciplines in the complete value chain is crucial. We experienced a great pro-active and open culture within the consortium to cooperate and challenge each other and our work. All participants were really open to support the NTCP trials and share their thoughts and insights. A great match of mindset with our own philosophy.
Second, current infrastructure and technology at sorting plants can be used to further separate film streams in more mono-material like streams. Combined with other steps in the QRP, such as hot washing and extrusion, results in in a range of higher value applications for recyclate. The resulting milestones are now being taken into industrial scale trials and we can’t wait to see this potential being taken mainstream.
Learn more about CEFLEX Quality Recycling Process for flexible packaging.
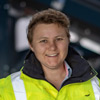
Martine Brandsma,
Director, National Test Centre Circular Plastics (NTCP)