If there was a simple one to 10 scale that plotted progress towards achieving a truly circular economy for flexible packaging, where would Europe fall? Nikola Juhasz laughs as she ponders the question. She is global technical director for sustainability at Sun Chemical, an international supplier of pigments, printing inks, coatings and adhesives, primarily to the packaging industry. “Well, we’ve certainly taken more than our first steps,” she says. “Some locations are further along than others. But probably something under a five.”
Working to move the needle on this complex and multi-layered task is CEFLEX, whose 160+ stakeholders span the entire packaging value chain, from baby food producers to waste and recycling giants. Belying Juhasz’s dedication to the cause and the “truly global” nature of her role, she says she recently participated in a CEFLEX workshop held at the unsociable hour of 3am. (Juhasz is US-based while CEFLEX stakeholders are predominantly located in Europe).
This particular workshop was centred around defining a common position on the collection of flexible packaging within Europe, in line with a circular economy. “There were a variety of views that were expressed during the workshop and so the position statement was carefully constructed. But it summarises the importance of having separate collection streams,” she says. Indeed, if the name of the game is keeping resources in the loop for as long as possible, you’ve got to first capture those resources. Seems pretty fundamental. But why is it preferable to have segregated curbside collections of this type of packaging? And before we get to that, what does a senior executive at a chemical company know about recycling anyways?
Quite a lot, it turns out. Juhasz has nearly three decades of experience in the chemical engineering industry and holds a Ph.D from MIT in the subject. She’s been at Sun Chemical since 2016, and has extensive experience in printing inks for packaging. Since 2020 she’s been responsible for technical sustainability initiatives and strategy with a particular focus on flexible packaging, and is also heavily involved in several cross-industry organisations to push forward the circular economy agenda.
On separate collection being preferable, Juhasz explains that, “The more you do that, the less stress you put on the subsequent steps in the process. You avoid cross contamination between different streams, which would negatively impact the quality of the recyclate.” Achieving true circularity, she stresses, means being able to use that recycled packaging to, ultimately, make new packaging. “If you have to downgrade because you’ve got contaminated components and incompatible wastes, well then you’re not really achieving that circular concept. We’ve got a lot of material that can be used to make roadways, and outdoor equipment, for example, but you can’t really drive it back to the packaging market.” Which, along with other circular strategies, is exactly what Sun Chemical is trying to do.
They have been sourcing recycled plastics on the open marketplace, for use in their products. For example, plastic materials are used as binders in their inks, coatings and adhesives formulations. But it’s essential that this recycled plastic material is relatively high quality, says Juhasz. Monitoring sustainability across Sun Chemical’s entire value chain is important to them. But from a purely economic point of view, if they’re in the market for high quality recycled resin, they’ve got to work closely with the reprocessing industry to create the conditions necessary to produce high quality recyclate, which that resin is derived from. “We want to ensure that packaging materials can be reused in new packaging applications, and we need to design the components that we provide for that packaging (inks, coatings, adhesives) in order to enable that recyclability – or at least not to interfere negatively,” says Juhasz.
Sun Chemical creates the inks that make a product stand out on a shelf, the coatings that make them resistant to moisture or sunlight and the adhesives that hold our crisp packets and pet food pouches together. Although they’re not creating flexible packaging themselves, they’re nevertheless employing a number of strategies to help reprocessors deal with it when it reaches end of life. “We’re looking at lightweighting strategies. Selling, for example, coatings with barrier properties, whether that’s moisture barriers or gas barriers that would replace plastic layers within a multi-layer structure. So this is a way to remove plastic; it’s not even part of the package to begin with.”
They’re also working on inks that can be cleanly removed in the recycling process, as contamination through colour can be problematic. “We have engineered inks that can be cleanly removed from certain films, without bleeding into recycling wash water. Also inks that are resistant and stay on those films, depending on what is needed for a particular type of packaging application and recycling process. Employing these technologies is an example of how we’re listening to what that part of the value chain was saying.”
Juhasz represents perhaps one of the most important but least visible industries in the puzzle that is the circular economy for flexibles. Adhesives hold our packaging together, inks are essential for marketing and labeling, and coatings provide functionality. They’re incredibly useful in our modern world, but their key characteristics – stickiness, endurability, strength – cannot become their downfall. “We need to ensure that the properties of the products we’re delivering do not become barriers to circularity,” says Juhasz.
But Sun Chemical is but one stakeholder on this circularity mission and Juhasz is well aware.
“The sustainability issue is not one that can be solved by any particular player. It’s really going to involve the entire value and supply chain coming together. So we take very seriously the importance of participating in organisations like CEFLEX.”
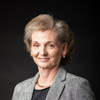
Nikola Juhasz,
Sun Chemical