Recycling Technologies in Focus: Scaling Delamination for Circular Flexible Packaging. Interview with Sebastian Kernbaum, Managing Director, Saperatec
Delamination is gaining traction as a key enabler for circularity in flexible packaging – offering the potential to unlock high-quality recycled content, reduce environmental impact, and support compliance with the EU’s Packaging and Packaging Waste Regulation (PPWR). We spoke with Sebastian Kernbaum of Saperatec to explore the technology’s benefits, key enablers for scaling by 2030, and barriers to reaching its’ full potential.
What are the key benefits of delamination in helping companies comply with PPWR and advance the circular economy for flexible packaging?
Delamination is a form of advanced mechanical (physical) recycling specifically designed to treat multilayer materials and other complex flexible packaging formats. It enables the recovery of high-value materials in solid form, preserving their quality and making them suitable for reuse in demanding applications.
One of the major advantages of delamination is that recovered materials retain properties close to virgin polymers, meaning they can be reprocessed using existing technologies, especially into film-based applications. This helps companies meet PPWR recycled content targets, while also contributing to overall recycling rate obligations, since nearly all materials can be recovered in solid state.
At Saperatec, we go a step further by integrating a decontamination step into our delamination process. This removes (volatile) organic compounds and other residual contaminants from polymers, producing post-consumer recycled (PCR) regranulates that meet CosPaTox requirements for sensitive applications. We’re also working to validate this approach for food-contact applications, which would be a major step forward for circular packaging systems.
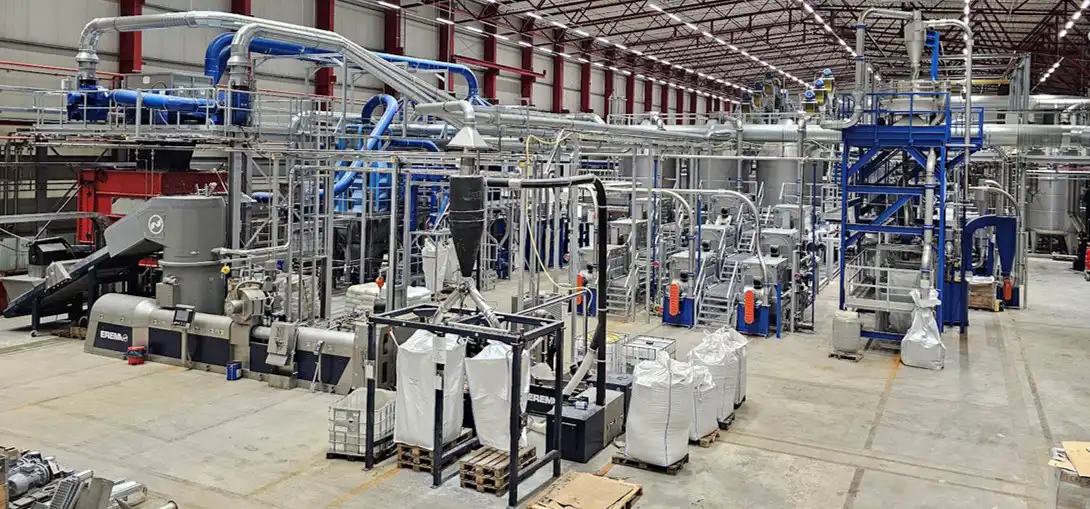
Saperatec site in Dessau-Roßlau, Germany, where the company operates an innovative recycling plant for beverage carton waste and other composite packaging waste made of plastic, aluminum, and paper.
What are the critical enablers needed to maximise the impact of your technology in Europe by 2030?
A key enabler is the early and proactive adoption of advanced mechanically recycled materials – before PPWR obligations for recycled content and recycling rates fully come into effect in 2030.
Testing, validation, and integration of recycled content into new packaging formats takes time. For films and hygiene-sensitive packaging, development cycles can range from 18 to 36 months. That means companies need to start now to ensure solutions are market-ready by the time compliance becomes mandatory.
Currently, there are too few large-scale projects beyond the final investment decision stage to meet the expected demand in 2030. What we need is a “start now, scale fast” mindset, supported by a deep collaboration across the value chain, from technology providers and film producers to converters, fillers, and brand owners.
CEFLEX is an important player in stimulating this discussion and targeting advances for flexible packaging and even beyond.
It’s also essential for industry to recognise that advanced mechanical recycling involves higher costs than conventional methods; but still remains significantly more cost-effective and environmentally friendly than chemical recycling. A shared understanding of this value–impact balance is needed to drive investment and adoption at scale.
Delamination is an advanced physical recycling process enabling recovery of high-value materials in solid form, preserving their quality and making them suitable for reuse in demanding applications.
What are the biggest challenges or barriers to scaling your technology, and how can they be overcome?
The current economic climate poses the biggest short-term challenge. Low virgin polymer prices and weak market conditions for recycled materials have led many companies to delay or cancel projects involving recycled content. This puts progress toward 2030 PPWR goals at serious risk. A more stable and supportive policy and market environment is needed to de-risk investment in advanced recycling infrastructure.
Additionally, clear, harmonised guidelines for the safe use of post-consumer recyclates – both for food and non-food contact – would accelerate uptake. Right now, the lack of clarity and the growing number of internal brand-specific requirements are adding complexity to product development for recyclers and converters alike.
Collaboration, transparency, and early alignment across the value chain will be key to overcoming these hurdles and unlocking the full potential of delamination technologies in the circular economy.
Sebastian Kernbaum,
Managing Director, Saperatec