A Quality Recycling Process for flexible packaging from CEFLEX and stakeholders shows product yield and quality for high value applications suitable to replace virgin polymer grades using mechanical recycling.
A lot can be delivered today with existing sorting and recycling technologies – if only the required infrastructure was in place to unlock its full environmental and economic potential.
Collaborating together in the Sustainable End Markets workstream, CEFLEX stakeholders aim to bring a Quality Recycling Process to market – delivering recycled polymers for higher-value end market applications than currently commercially available.
A new e-booklet draws on interviews, presentations and processes to explore and profile the Quality Recycling Process from several perspectives and give insights from those who have rigorously tested its potential.
Through the power of their value chain collaboration and expertise in the waste management of flexible packaging, today they are able to prove that
With this milestone reached, the CEFLEX workstream is moving forward into industrial trials to build the business case for investment in the infrastructure which can leverage this process into a mainstream solution to keep the materials in the economy at the highest value possible.
The Quality Recycling Process Action Team run the technical ‘proof of concept’ for household collected post-consumer flexible packaging Post-Consumer Waste (PCR) which demonstrates:
- Recycling back to a wider range of non-food flexible packaging is possible – including more demanding applications through mechanical recycling via the Quality Recycling Process.
- The Quality Recycling Process produces film grade quality rPE and rPP polymers appropriate for non-food flexible packaging by applying near infrared (NIR) sorting by polymer and color, followed by hot washing and extrusion with extra filtration and deodorization.
- As a real breakthrough, film grade recyclates for natural rPE and all color rPP can be obtained at good product yield and quality and with mechanical and processing properties (i.e. film extrusion process) which make these materials suitable for replacement of virgin polymer grades.
Data from industrial trials running in 2020-21 will assess the economic viability of the process and a business case for investment in necessary infrastructure.
Consult the e-booklet for a range of perspectives and experiences about boosting value and keeping materials in the economy.
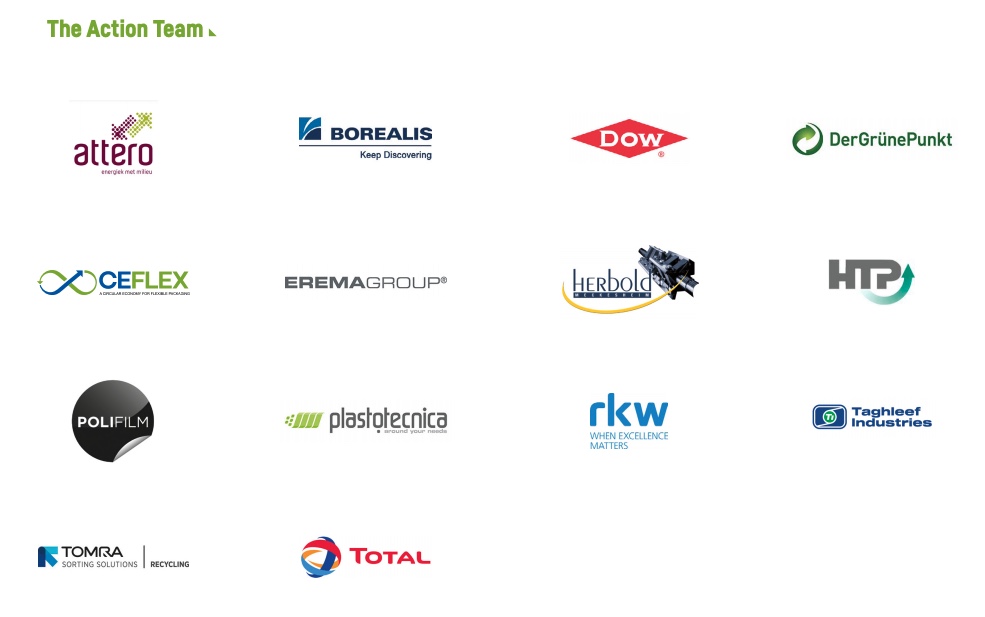