Many designers lack the information to ensure their flexible packaging can be recycled, but a new testing program is working to plug these knowledge gaps by independently verifying the ideal mix of materials, according to Dr Bronagh Millar, from the Polymer Processing Research Centre at Queen’s University Belfast in Northern Ireland.
What’s standing in the way of more flexible packaging designs from becoming recyclable?
It’s not easy being a flexible packaging designer because they are dealing with different people asking them to achieve different goals – whether that’s a products’ aesthetics for marketability, extended shelf life, green credentials or sustainable sourcing. There are so many different things at play and the designer is faced with a difficult balancing act trying to fulfill them all.
In the current climate, designers probably feel very exposed when making decisions because they are unaware if some choices result in a package becoming incompatible with recycling. The information isn’t there to help them know whether or not a package is going to make it through the whole life cycle from being put on the shelf to ending up in a recycling bale. Having design guidelines are really important to help designers in a company promote packages that are circular and sustainable.
You’re helping to deliver a new testing programme with CEFLEX, ensuring it is independent, credible and robust. How will the research on how different materials and elements in a flexible packaging structure affect sortability and recyclability help the sector adopt more circular designs?
The approach we are taking in this project is to engineer a base material from the types of polyethylene and polypropylene that are represented in the marketplace today. What is being sorted into bales for recycling can be very different across sites in Europe, from one day to the next. Instead of taking one of these bales and having all its variability, we will focus on what materials are being placed in the marketplace and then produce a blend, a larger volume average of those materials, as a clean form of recyclate that doesn’t have any contamination. This means we can look at the effects of those different elements in the flexible packaging structure against the engineered based material and generate accurate data on its impact on recycling.
This is being done through laboratory testing with a two-phased approach – first, there is a pre-screening phase which will benchmark which different elements in flexible structures have effects on the quality of recycling. We will then take those benchmarks and put those through a more robust set of mechanical testing protocols which are going to be done by a number of laboratories across Europe.
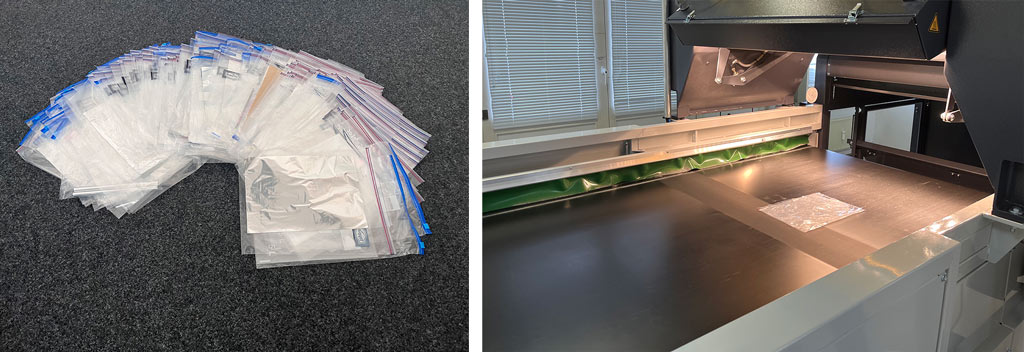
200 samples were tested to obtain an understanding of the abilities and limits of NIR sorting technology
How will the tests on these control base materials generate the data for circular flexible packaging designs?
That is why we designed a set of experiments to really hone in on what that percentage of material could be in a package to have limited impact on recycling. There are a lot of elements that we’re interested in and a lot of different structures, sizes and types, as well as barrier materials, inks, adhesives and metallisation.
Why is it so important that this testing is conducted under an independent, scientifically-based approach?
It’s critical we take this approach because the data and testing could otherwise face criticism for being aligned to industry or certain materials and companies. That is why it’s very important we have an overview of the process to ensure the credibility of the end results. The independent approach we are taking ensures that both positive and negative data is being examined and that we end up with a true understanding of the impact of different materials and structures on the quality of the recycling stream.
The other benefit is that we know it will be representative of what is happening across the market. We are able to choose the elements and materials that are to be studied and determine are they truly reflective of the different flexible packaging formulations on the marketplace. If it was done in a way where other stakeholders produce that information there is a risk the testing could lose that breadth of material analysis.
We also helped describe how we think the data should be generated in the first place, and what tests should be undertaken to do that, but we don’t actually perform the testing – we sit back from an independent perspective and look at the results that come out. Then we help CEFLEX assess what is the effect of various different structures on mechanical recycling of polypropylene and polyethylene.
How will these independent results be used to update CEFLEX’s ‘Designing for a Circular Economy’ (D4ACE) guidelines?
Every piece of data that we look at will go towards updating the D4ACE guidelines. When they were first launched there was some criticism that when they were developed there was a lack of robust data behind them, that they evolved from the best understanding and commercial practices at that time. But with all of the information now being generated this feeds in to a robust guide, which is a very long, and expensive process, involving the cooperation of many CEFLEX stakeholders.
What will be the wider benefits for the flexible packaging sector from these experiments and the updated D4ACE guidelines?
I would hope that it means we can reduce the amount of materials that are put on the marketplace that cannot be handled in a circular way and decrease the amount of items destined for landfill. There are a lot of products that are never going to be recycled because the way they have been designed mean it’s just impossible for today’s infrastructure to handle them. CEFLEX is able to tip the balance and promote more sustainable packaging designs and encourage them through the marketplace because of its size and depth of stakeholders. What they produce is also available for everyone and that is very important to have as wide an impact as possible.
Dr Bronagh Millar, Queens University Belfast