Quickfire questions to Graham Houlder and Dana Mosora about the path ahead for flexible packaging
What are the biggest roadblocks to a coherent circular economy?
Secondly, recognising chemical recycling as a critical piece of the circular economy for plastics puzzle and commercialising it at scale for required capacity in the coming three years.
Thirdly, the amount of debate and energy still spent on design for guidelines for (flexible) packaging plastics. We know what needs to be done here. The focus needs switch towards developing end market pull for recycled plastics by making them financially competitive against the virgin equivalent.
How must the flexibles segment respond to these challenges in a practical way?
CEFLEX stakeholders in the front part of the value chain i.e. material producers, film converters, brand owners, need to accelerate demand for recycled materials by using them in their plastic grades, flexible packaging and products on the market.
EPR needs to facilitate this by ensuring recycled plastics are always a better business proposition than a virgin equivalent by modulating the subsidies for these materials to allow them to do so.
Parts of the collection, sorting and recycling value chain – now including many material producers – need to invest in the required infrastructure to deliver the CEFLEX circular economy vision. EPR systems (led by the brand owners) need to underwrite these investments in developing the needed collection, sorting, recycling capacities of mechanical and chemical recycling by reducing the investment risk for these companies through longer contracts at a guaranteed rate of return on their investments.
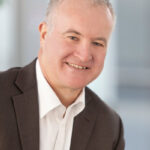
Graham Houlder,
Project Coordinator, CEFLEX
What are the biggest roadblocks to a coherent circular economy?
In the practical case of recycling, we need to explore how we switch from a quantity to quality approach for recyclates returning to the circular economy. Industry initiatives to drive design guidelines, recycling technologies and new processes is largely happening and progress being made, which is encouraging.
But investment in new infrastructure is necessary. The recycling industry is not a high profit one… not yet! Consequently, recyclers can’t take the required risk to implement the required changes. Legislation like the European Green Deal and focused investments need to accelerate this.
How must the flexibles segment respond to these challenges in a practical way?
QRP produces recycled film grade polyethylene and recycled polypropylene which can be used in non-food flexible packaging applications, such as: collation shrink and pouches, labels and other type of sacks and bags. It also produces valuable Injection molding grades of recycled polyethylene and a mix of recycled polyolefins.
Our pilots and business case tool show that the time is right for the value chain to invest in such quality recycling plants and mainstream its significant potential.
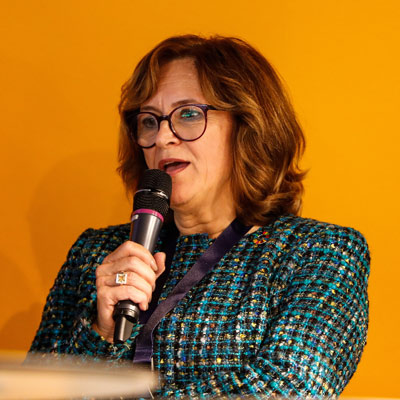
Dana Mosora,
Consultant, CEFLEX